How to insulate the nozzle (optional)
A cold nozzle can lead to a handful of issues and derail your experiments. Here's a bit more insight into how to avoid a cold nozzle.
Cold Nozzle
Environment
While the Heaters effectively melt the material inside the barrel, the nozzle is the point where that molten polymer extrudes and meets the room temperature environment. We recommend installing the machine in an environment that does not have any sudden temperature fluctuations (cold warehouse) and has a consistent room temperature (18-23℃).
Positioning
Another important factor is to set up the Fans and the Nozzle correctly.
Figure 1 showing the correct fan positioning:
- attached cover plate
- symmetric positioning
- fans are pointing towards the flow of the output
Figure 1. Correct fan positioning
Figure 2 showing an incorrect fan positioning:
- missing cover plate -> might cause more nozzle cooling
- not symmetric -> might cause filament waving
- fans are pointing upwards and/or towards the
- nozzle -> might cause additional nozzle cooling
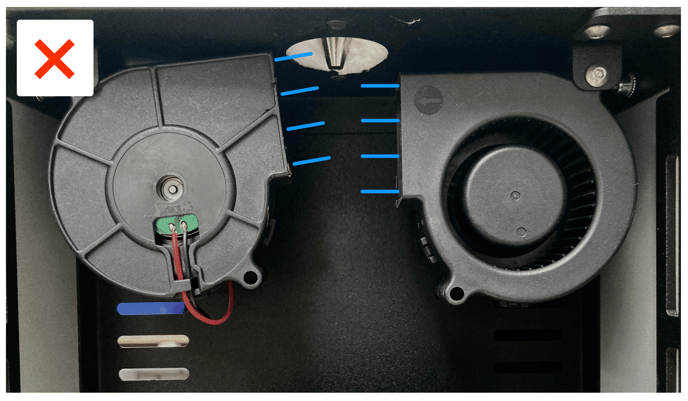
Figure 2. Incorrect fan positioning
Material
However, even if all the environmental and installation details are correct and safe, there are still some materials that are extremely sensitive to sudden cooling. Highly crystalline materials tend to have the most issues with this. For example, we have found that HDPE is sensitive to directional cooling so we created a circular fan prototype.
Another example is rPET as is shown in an older report. The solution in such instances is found below.
Insulation
To keep the nozzle warm enough for these extrusions, it can be surrounded with glass wool. Since it's such a small amount, users can just repurpose some wool from around the Heaters as shown below.
![]() |
![]() |
- Use protective gloves and long-nosed pliers to carefully and securely place a small segment of insulation wool around the nozzle!
- Ensure that the wool does not reach lower than the tip of the nozzle!
The insulation wool used around the Heaters is Insulfrax LTX (128 kg/m3).