Understanding pressure, and tips to avoid clogging!
A neat overview of what happens inside the barrel when material goes through, and how to use the combination of speed, temperature, and material knowledge to achieve consistent flow.
Pressure
Without pressure there is no extrusion. Getting the right amount of pressure can be tricky, as well as keeping it consistent. The following two illustrations describe different extremes of pressure that result in bad output, while the third illustration shows the ideal scenario.
This article relates to the Flow Phase of a regular extrusion run, after we have introduced our Processing Material, but before we finetune the filament.
Flow before Finetuning!
Many users jump ahead to analyze their filament and try and spool it without realizing that they never achieved a consistent flow. Without a good flow we cannot achieve quality filament, and might even risk a clog!
As always, we gather our data and knowledge from a multiple of sources and plenty of preparation:
Plan approach and set expectations based on: | Filament Maker
|
+ |
Material
|
↓ |
↓ |
||
Refine process and make adjustments based on: | DevoVision
|
+ |
Evidence
|
High pressure
This is where the material does not melt sufficiently. Usually occurs with pellets though it can be with any form of material. Additionally, this can be the case when using additives especially mechanical additives that do not melt.
The material(s) perhaps partially melts but not enough to smoothly flow out of the nozzle. In better situations, this means we end up with solid particles in the output, however in worse scenarios the solid material can agglomerate and even lead to a clog. In such cases, the motor struggles to turn the screw, which shows up in DevoVision as high motor current, spikes or on the FM interface as an Error Message.
Features of high pressure:
- high motor current > 1500-2500 mA
- low flow / low output
- unmelted particles in output
- risks of clogging at the nozzle
Low pressure
On the opposite end of the spectrum, the material melts too much or quickly. This situation often happens with finer material forms such as powder or shredded material, however it can happen with sensitive materials in pellet form, too. Though it might not degrade or burn, the material will melt too early causing very low flow, and it risks partially melting and even clumping in the Hopper.
Features of low pressure:
- low motor current < 1500-2500 mA
- risk of clumping in Hopper
- liquid material pooling in the barrel
- little or no output, often just drops of plastic
Consistent pressure
In between these two extremes we have the sweet-spot. The material enters the Hopper solid, and only begins to melt closer to H4 and even H3. It's not until H2 that we have a fully melted material completely supported and pushed forward by all the solid material behind it. This will also be evident in a continuous flow out of the nozzle.
Features of consistent pressure:
- consistent motor current
- good pressure build-up
- solid material pushing liquid material forward
- consistent liquid output
Tips to avoid clogging
As we have seen with both the high pressure and low pressure scenarios, clogging is a risk. The following are some helpful reminders that help keep the risk of clogging to a minimum.
Log the data!
Having DevoVision open means you can track any internal parameters and data. You can notice if there is an increase in pressure or lack of pressure from the Extruder Current graph. You can check how the Heaters are performing. You can see if there is a spike in RPM or if the machine is struggling with the feeding material. All of these (paired with the visual output) are indicators to help you identify when everything is going well, or when there is a risk of a potential problem.
Visible inconsistency in the pressure, which will most likely negatively affect the output:
Steady Motor Current and RPM, resulting in consistent pressure:
Keep the nozzle insulated!
Since the nozzle protrudes from the FM, it is important it does not experience any sudden temperature changes. We always remind users not to turn the fans on the nozzle. As an additional safety measure, it can be further insulated.
Material size vs nozzle diameter!
Our default set up is a nozzle with a 4mm internal diameter. This is also why we must not feed any material larger than 4mm in diameter. If there are any issues with the material melting, full pellets can still exit the nozzle. This is not the case with the 3mm and 2mm nozzle sizes. They come with added benefits as well as risks. Ensure you know what nozzle size you are using!
In general, we recommend using the 4mm nozzle when testing new materials to minimize the risks!
Operate at the correct temperatures!
This means waiting for all four Heaters (especially H1) to meet the set temperatures. On DevoVision, this is simply shown as the blue line 'Temperature' meeting the yellow line 'Set Point'. The green line is 'Duty Cycle' indicates how much the Heater has to work to reach the set temperature. In the example below it takes Heater 1 almost 45 minutes to precisely reach 400℃ from room temp.
Ensuring that you introduce the correct materials at the correct temperatures will avoid most issues. This is also directly linked to transitioning.
Transition slowly!
Transitioning from material A to material B happens in a specific temperature window. As the example illustration below shows, if both material A and material B remain in the barrel and the temperatures are raised or lowered outside of the transition window, clogging might occur. This is why we recommend considering the residence time of the material, looking for visual evidence of a full transition, and raising or lowering temperatures slowly and safely while monitoring DevoVision.
We have more tips on transitioning safely (with illustrations) here!
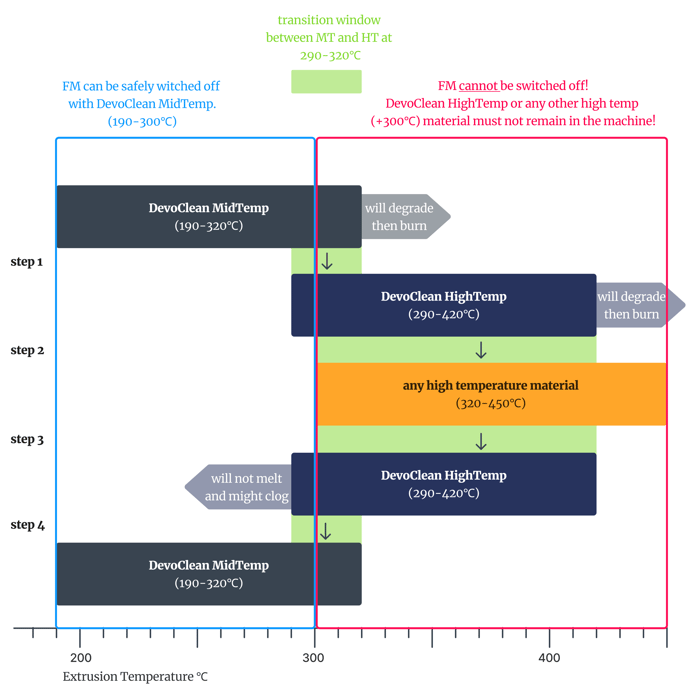
step 1: safe transition from MT to HT to be able to extrude at +300℃ temperatures
step 2: introduce the high temp processing material
step 3: when finished with processing material, purge it out with HT
step 4: transition down to MT to be able to safely switch off FM
Familiarize yourself with DevoVision and learn how to interpret the datalog graphs live.